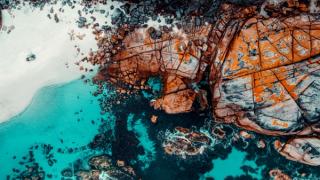
Climate Transition Plans: Decarbonisation is only one part of the puzzle
by James Balik-Meacher
View post
The Dangerous Substances and Explosive Atmospheres Regulations (DSEAR) first came into force in 2002 but many businesses are still falling short of the requirements. Whilst the number of breaches identified during lockdown has dropped, manufacturing companies continue to receive more than 65% of the notices issued, suggesting this is where help might be needed most.
Regulation 5 requires all employers and self-employed to assess potential risks to employees and others whose safety may be affected by the use or presence of dangerous substances in the workplace. This requires knowledge of the properties of substances, circumstances of the work, maintenance activities, effectiveness of risk reduction measures, likelihood of flammable atmospheres and presence of ignition sources, and scale of the anticipated effects.
The Health and Safety Executive (HSE) identifies dangerous substances as any substances used or present at work that could, if not properly controlled, cause harm to people from fire or explosion. Given that this includes such things as solvents, flammable paints, varnishes and dusts, as well as gases under pressure and corrosives, and the fact that manufacturing often encompasses a range of complex operations, we should not be too surprised by the attention the sector receives in relation to DSEAR.
However, Regulation 6 covering elimination or reduction of risks from dangerous substances, seems to be presenting a particular problem [1].
Compliance with Regulation 6 requires duty holders to consider the hierarchy of controls and where possible look to eliminate or reduce hazards at source before considering the use of engineering controls, administrative controls or personal protective equipment. It also calls for mitigation of detrimental effects from fire, explosion or other harmful physical effects.
In order of priority, consideration of risk control measures should include:
Whereas mitigation of detrimental effects should include consideration of:
Completion and regular review of risk assessments can be time consuming. Couple this with registration, regular maintenance and review of the physical and procedural measures in place, it is easy to understand why some businesses lose sight of where they are in terms of compliance with the regulations.
Here are five simple questions that you can ask yourself and those around you to spot signs of non-compliance:
If the answer is no, or you are unsure then why not contact us to find out how we can help.
Visit our Safety Advisory page to learn more about our services and how we can support you.
by James Balik-Meacher
by Peter Lo
by Melissa Birch, Tarra Tamang